COMPONENTES SMD
INTRODUCCIÓN
Desde hace ya algunos años, la tendencia general en la electrónica es que se abandonan los componentes tradicionales y se hace uso extensivo de componentes SMD
Un componente SMD (Surface Mounting Device) es un componente electrónico que se suelda diréctamente en la superficie de la PCB. Tradicionalmente, los componentes se montaban introduciendo sus patas por un agujero y sodándolas al otro lado de la placa. Ahora no hay agujero, sólo hay dos cuadraditos de cobre sobre los que se suelda diréctamente el componente. |
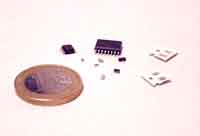
componentes SMD
|
inicio
Ventajas de los componentes SMD
Las ventajas principales de los componentes SMD se basan en su reducido tamaño y en la ausencia de hilos.
Son bastante pequeños (resistencias de 2mm de largo x 1 de ancho, y menos, y transistores e ICs incluso con 0.6mm entre las patas), y ahorran básicamente espacio y longitud de pistas de cobre. Esto es una gran ventaja porque se pueden hacer placas que ocupan la cuarta parte de espacio, reduciendo la longitud de las pistas. |
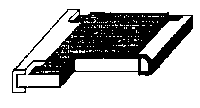
Resistencia SMD
|
Por otro lado, el hecho de eliminar el paso del hilo a través de un agujero supone lo siguiente: si existen 180 agujeros y la placa mide 1.5mm de espesor, se está ahorrando mínimo 27 cm de pistas, que son como cable malo sin apantallar. Hay que añadir la porción de hilo doblado que sobresale entre la PCB y llega al componente, por lo que pueden ser más, y que esta porción está expuesta a la óxidación. |
Condensador SMD
|
Ahora, en términos más científicos, la eliminación de las patas supone una mejora en la inductancia y en la resistencia parásita que ofrece el encapsulado. La inductancia parásita puede reducirse a 1nH, y las resistencias, de 5-25mOhm a 1mOhm. Esta cantidad puede parecer ridícula, pero no debemos olvidar el efecto Kelvin, que a altas frecuencias hace que los electrones se vean desplazados por los campos magnéticos, más lentos, y se vean empujados a los límites exteriores del conductor. |
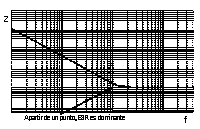
ESR en condensadores
|
Este efecto produce una disminución de la sección efectiva del conductor, y por lo tanto un aumento de la resistencia. Esto, para fuentes conmutadas donde se trabaja a 50-200kHz es un grave problema, porque se puede llegar a 0.1Ohm, y 2A producen una pérdida de 0.2V. Si tratamos de alimentar un integrado CMOS de 1.7V, las pérdidas son del 20%, lo que no es depreciable. |
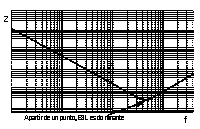
ESL en condensadores
|
En general, todo circuito de alta velocidad, bien sea digital, analógico o PWM debe usar SMD, ya que el comportamiento a altas frecuencias es mucho mejor, no hay patas de resistencias que hagan de antena, no hay inductancias parásitas tan grandes. Es incluso fácil de observar que las señales cuadradas son más cuadradas, con menos overshot y tiempos de subida y bajada menores. |
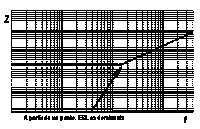
ESL en una resistencia
|
Como ventajas adicionales, son componentes que están preparados para las últimas tecnologías, y por ejemplo es habitual que soporten muchos tipos de ácidos, disolventes, limpiadores, y que sólamente con sumergir el circuito en acetona se eliminen los residuos resultantes de las soldaduras. En los componentes through hole esto no es norma, por ejemplo los electrolíticos no lo permiten, ciertos tipos de resistencias tampoco, los condensadores de película enrollada que no estén recubiertos de resina epoxi tampoco.
Los residuos de las soldaduras pueden ser higroscópicos y/o ácidos, por lo que es necesario eliminarlos, ya que pueden formar resistencias y condensadores parásitos.
También son más ligeros, por lo que son recomendados para áreas muy estrictas del diseño como aviación, competiciónes deportivas, armamento,...
inicio
Desventajas de los componentes SMD
Las principales desventajas están relacionadas con aspectos térmicos. El reducido tamaño implica que la superficie de disipación también es menor, y normalmente la resistencia térmica entre el interior del componente y el exterior es más grande.
Afortunadamente, estos efectos son perfectametne predecibles y con un buen diseño no tienen porqué afectar a la calidad del producto.
Empezaremos diciéndo que los componentes siempre sufren modulaciones térmicas en su valor. En todos se pueden medir, habitualmente se miden en ppm/ºC (partes por millón por cada grado Centígrado). Y la resistencia térmica también se puede medir, tanto en comportamiento estático como dinámico. Se mide en ºC/W, o para el caso de baja potencia, en ºC/mW.
Vamos a poner el ejemplo de una resistencia metal-óxido de carga de una etapa clase A en un aplificador de válvulas. Sufren variaciones de potencia bastante importantes, ya que pueden pasar de disipar 3W a disipar 1W en condiciones completamente normales. Las variaciones suponiendo Rtia(interior-ambiente) de 35ªC/W, (dato de resistencias de 4.3W de Welwin), la diferencia de temperatura entre reposo y máximo consumo son de 70ºC, esto unido a una deriva térmica de 350ppm/ºC suponen una tolerancia por motivos térmicos de un 24.5%, pudiendo causar una distorsión del mimo valor. Para altas frecuencias esto no tendrá grandes efectos porque la inercia térmica es grande, a pesar de que también la resistencia térmica es mayor que en estático (¿deberíamos decir...inductancia térmica?) Pero a frecuencias suficiéntemente bajas producirá una distorsión más que notable.
El caso de los componentes SMD es semejante. Los coeficiéntes térmicos dependen exclusivamente del material, tendrá el mismo coeficiente una resistencia de mtal en SMD que en through hole, pero estos componentes tienen mayores resistencias térmicas entre el interior y el ambiente.
De hecho en transistores de señal es obligado tener en cuenta que la potencia no viene delimitada por el transistor, sino por el encapsulado, y en el caso del SOT-23 (el más común) es de 225mW, cuando cualquier transistor acepta más de 300mW. Ahí es donde interviene la complejidad en el diseño. Es necesario utilizar un radiador, para evacuar el calor del interior del transistor. Pero ¿cómo se coloca ese radiador? Si mide 2 x 1 mm de ancho...
La solución está en disipar el calor a través de las pistas de cobre. Ellas mismas hacen de radiador, y si se desea incrementar la disipación de potencia de un transistor es necesario incrementar la superficie de la pista a la que está conectada el drenador o el colector. |
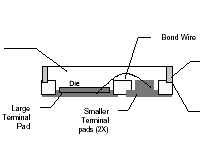
Transistor SMD de potencia
|
Es necesario tener en cuenta que también el encapsulado está sujeto a variaciones de longitud por motivos térmicos, por lo que los encapsulados deben tener los mismos coeficientes de dilatación que la fibra de vidrio. Esto es algo que los fabricantes lo tienen muy en cuenta y ya los fabrican así, porque si no se reduce la vida útil del circuito, ya que las soldaduras sufren estrés mecánico y fatiga.
Como consecuencia de éste punto, la mayor causa de fallos en dispositivos SMD es el estrés mecánico. Es importante evitar la posibilidad de un shok térmico durante el proceso de soldadura. Es necesario un precalentamiento del componente entre 80 y 120ºC, y que la diferencia de temperatura entre la pista y el componente no exceda los 150ºC. Posteriormente, debe enfriarse al aire.
La última desventaja es que no son fáciles de encontrar en comercios, normalmente se encargan por catálogo.
inicio
Resumen
Las ventajas se centran en un mejor comportamiento ante señal, dada la redución de los efectos parásitos, la reducción del área de PCB y la longitud que debe recorrer la señal. Las desventajas, en una mayor dificultad en la fabricación (aunque se ahorra el tener que hacer agujeros en la PCB), y en los efectos térmicos en los componentes, desde estrés hasta funcionamiento en potencia.
inicio
|