Una de las primeras dudas que asaltan a quien se construye unas cajas es la de si usar tornillos o usar cola de carpintero. Nunca he tenido problema en usar los dos. Y como se podrá observar a lo largo de la construcción de la caja, no tengo ningún problema en poner un gran número de ellos. En la foto, los primeros refuerzos y los agujeros de los tornillos de las tapas, cada 5 cm. |
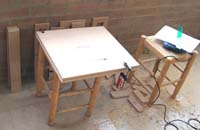 |
Es importante que los tornillos queden al ras, que no sobresalgan nada en absoluto, y para eso se puede usar una broca especial que hace los avellanados. En la tabla exterior los tornillos no deben hacer rosca, así es como realmente aprietan una contra la otra.
Partimos de una estructura con tres caras montadas, permite trabajar muy cómodamente, que es algo esencial para hacer un buen trabajo. Si se trabaja con dificultad llegan los errores, porque están ocultos o porque generan nervios y éstos generan olvidos.
|
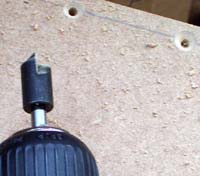 |
La estructura de los refuerzos que había pensados era como los de la derecha. Con unas paredes de mayor grosor hubiesen sido suficientes, pero al tener sólo 16mm fue necesario añadir más, sin ellos el timbre de la caja al golpearla no da la impresión de solidez.
También recomendaría menos originalidad en la construcción y ceñirse a las estructuras matrix, facilitan la construcción. |
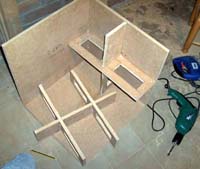 |
En la foto de la derecha se puede apreciar cómo fue necesario reforzar los bordes de los paneles para evitar que abriesen cuando se metían los tirafondos empleados para sujetar las tapas (4x45mm), a pesar de hacer previamente un agujero de 2.5mm.
Para ello hice agujeros de 1.5mm y metí un tirafondo de 2.5x19 entre cada par de agujeros gruesos, así hacían presión y el DM no se abría por por la mitad. Me tocó rellenar con cola y utilizar gatos.
Es una de las peores impresiones sacadas del DM, que la manera de romperse es muy dependiente de la dirección. |
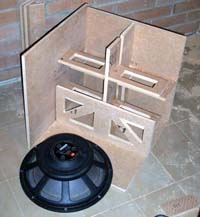 |
Una cosa clara es que cuando se trata de despegar dos trozos de DM encolados se partirá antes el DM que la cola, y se partirá por el medio de la tabla, quedarán dos iguales pero de menor espesor.
Todos los refuerzos están sujetos mediante tornillos. Los propios refuerzos están reforzados con tornillos para que no se abriesen con la presión que hacían los tirafondos al entrar. |
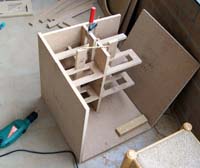 |
La familia de los refuerzos va creciendo poco a poco. El método para ir eligiendo sobre la marcha dónde poner más refuerzos fué símplemente ver en los laterales la "densidad de apoyos" (nº de apoyos por área), y donde había un hueco libre se ponía algo.
También se trató de que los refuerzos se apoyasen entre sí, para dar una mayor solidez al conjunto. |
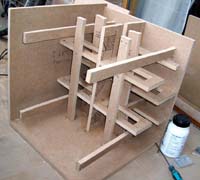 |
Lógicamente los refuerzos deben funcionar en las tres dimensiones, de nada serviría el trabajo si se dejan dos caras sin reforzar.
Al cortar un tablero con medidas más o menos grandes es normal que sobre bastante, y que estos trozos no se puedan aprovechar. Una manera de darles uso es hacer listones con la longitud interior y usarlos de refuerzo. |
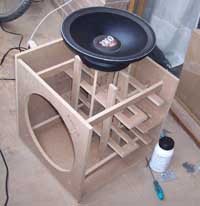 |
Uno de los refuerzos previstos era para sujetar el motor magnético por detrás, así que saqué mis propias medidas y pensé en una estructura que haría un poco de todo, sujetar el imán como si fuese una parte más, pero a la vez que hiciese de refuerzo para la caja.
Los esquemas de JBL eran bastante pobres, sólo indicaban tres medidas (ancho exterior, ancho del agujero y profundidad de montaje) y costó un cierto tiempo y algunos intentos acertar. |
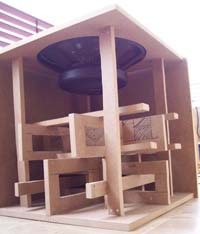 |
La estructura elegida para sujetar el motor se puede ver a la derecha. Era importante no tapar los agujeros de ventilación del motor, esto crearía compresión y es uno de los fenómenos más nocivos que puede haber en el audio.
A esta estructura se la añadirían posteriormente otros refuerzos conectados entre sí |
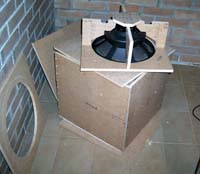 |
Aunque en este diseño no es muy importante la resonancia del chasis, en muchos altavoces está presente de manera más que evidente, y tratar sus efectos puede tener como consecuencia una respuesta diferente.
Los síntomas de la resonancia del chasis son un pico en la impedancia, y un aumento del SPL a partir de la frecuencia a la que se muestra ese pico. En la gráfica mostrada a continuación... |
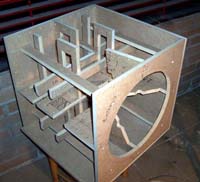 |
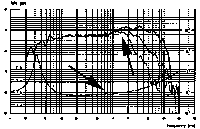 |
... podemos ver esos dos fenómenos. La flecha inferior indica un pico causado por la resonancia del chasis, y a partir de ahí la respuesta crece unos pocos dBs. |
Por encima de esa frecuencia ya no se transmiten las vibraciones al chasis. Es algo a tener en cuenta a la hora de hacer una caja, aunque lógicamente no es nuestro caso ya que no llegaremos a reproducir frecuencias tan altas. |
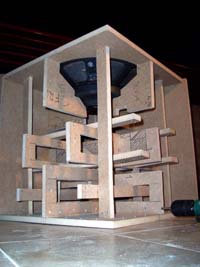 |
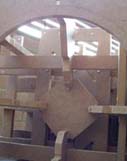 |
A la izquierda: foto mirando dentro desde el frontal,
A la derecha, el bloque del frontal con los refuerzos, y cómo encaja en el resto de la caja. |
|
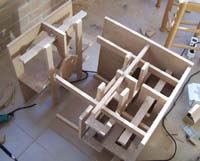 |
Aquí se puede ver cómo la estructura ya está montada y cómo tamién crea una firme sujeción para el motor.
Si hay que hacer correcciones, una lima de madera puede ser suficiente, una amoladora también puede servir. Piedras esméril mejor no, se llenan los poros con serrín y se puede inutilizar la piedra. |
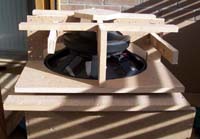 |
Estaba previsto que el bloque tenía que hacerse fuera y luego encajar a la perfección en la caja.
Era la única manera de comprobar que iban a sujetar de manera eficiente el altavoz, sin holguras y sin que no encaje, y sobre todo: de poder corregir cómodamente si no encajan a la primera. |
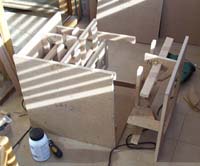 |
Aquí a la derecha puede verse cómo no tuve ningún pudor en poner tornillos, aunque en éste lateral ya había muchos que ya estaban atornillados.
Una vez montado el frontal con su grupo de refuerzos ya se pudo empezar a poner el resto de los laterales.
La caja va tomando forma y volumen, y es en éste punto cuando uno se empieza a dar cuenta del tamaño real, pero la masa todavía no es tan alta como será. Por entonces el peso era grande, pero todavía se podía levantar. Con la segunda caja y el altavoz ya no es posible. |
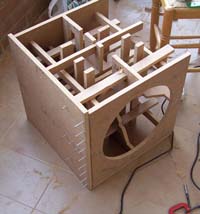 |
Uno de los tableros quedó cortado un poco más corto de lo debido, por lo que tuve que emplear pasta de cola con serrín para rellenar el hueco que iba a dejar. Estoy plenamente convencido de que esta pasta es más dura que el propio DM, así que no hay ningún problema en usarla en todas las partes que sea necesario.
Al comprobar la dureza tras el secado se corrobora lo anterior. |
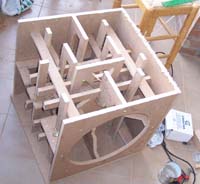 |
Aquí se puede apreciar el número tan exagerado de tornillos. Sólo para la caja interior se utilizaron 320 tornillos de 4x45, y aproximadamente 400 tornillos de 2,5x19. Desde luego el taladro ayuda, apretar más de 700 tornillos en poco tiempo es causa casi segura de tendinitis.
No se deben apretar del todo los tornillos hasta que todos hallan entrado en su rosca. SI no se hace así es muy posible que alguno no encaje enb el agujero y si tiene que hacer agujero partiendo de cero romperá el DM con total seguridad. |
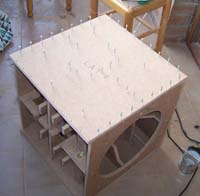 |
También había que ir pensando cómo sujetar el altavoz a la caja. Los tirafondos hacen rosca en el DM, pero a la tercera vez que se saca el tornillo la rosca se desgasta y ya no sirve. Es posible que halla que mover el altavoz, o modificar algo del interior, etc... y tiene que poder moverse. |
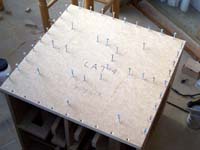 |
Sólo había trabajado con DM otra vez, y utilicé unas varillas roscadas hembra pegadas al interior del DM, pero aqui iban a soportar un altavoz de 7 kilos que iba a generar unas presiones muy elevadas. Una primera idea fué usar balancines para las lámparas, pero no fue posible.
Opté por hacer unas rocas en unas pletinas de metal y atornillar las pletinas a la caja. El resultado no pudo ser mejor, y con la ventaja de que si una rosca no encaja se puede meter diréctamente el taladro con baja velocidad y el macho de la rosca para hacerla justo en el lugar y dirección que convenga. |
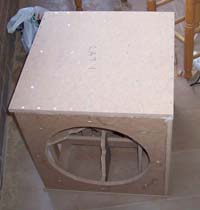 |
La caja ya empezaba a dar una idea de cómo de grande iba a ser.
Empleé dos conectores que tenía por casa. El cable se trata de un cable de red de 220V de 2,5mm^2, cuyo aislante es una espuma muy densa pero no es PVC. Se trata de cuatro pares trenzados. Esto hace un área de 10mm^2, lo que da una capacidad para soportar 100 Amperios. La resistencia ofrecida por el cable es ínfima. |
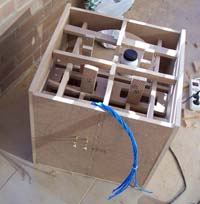 |
Una de las técnicas que mejor resultado me han dado es la de hacer una arandela de silicona entre el altavoz y la caja. En este caso habría que tener en cuenta también los apoyos del motor.
El proceso es el siguiente: se debe forrar la superficie que va a recibir silicona con cinta de embalar de polipropileno. |
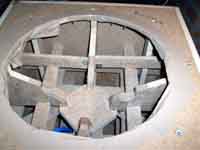 |
Es importante que sea de polipropileno porque la silicona no pega en él. Además se puede untar la superficie con una fina capa de cualquier aceite no volátil, esto facilitará que se despegue mejor.
Se debe cubrir con cinta cualquier sitio donde se vaya a poner silicona. Lo siguiente es poner silicona de forma abundante. Luego la aprisionaremos y cogerá la forma adecuada. |
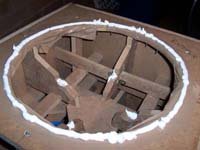 |
Y cogerá la forma adecuada con el molde adecuado, no hay nada mejor que utilizar el propio altavoz. La silicona quedará pegada al altavoz. También se puede hacer al revés, dejar la silicona pegada a la caja y forrar el altavoz, pero la silicona no pega bien en el DM, de hecho la porosidad del DM seca la silicona y absorve todos sus aceites.
Se debe apretar el altavoz, pero no tanto como para que toque en el fondo. |
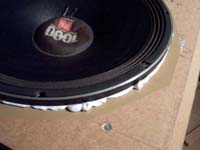 |
Debemos recordar que esta arandela no sólo hará que no salga aire, también hará que no se transmitan vibraciones a la caja.
Conviene dar una mínima forma a la silicona antes de que seque. Es aconsejable guardar el pegote de silicona sobrante cerca de la caja (preferiblemente en un entorno ventilado) porque así tendremos una referencia de cómo se seca en ese entorno. Cuando el pegote esté seco podremos quitar el altavoz y la silicona sobrante. |
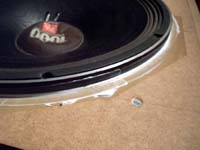 |
Tarda mínimo un día, si es verano, lo preferible es dejarlo dos o tres.
Aquí podemos ver el resultado. La silicona deja una arandela perfecta que encajará en el frontal. No puede haber mejor molde, y es una buena idea dejar esta arandela pegada a una de las partes porque si se mueve un poco no encajará tan bien. |
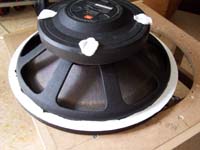 |
Una última mirada al interior de la caja. Me sobraban dos listones y decidí añadirlos en un último momento.
Ya se acerca el final de esta caja. Lo último antes de cerrar definitivamente, aparte de comprobar que todo está bien sujeto y que no nos dejamos ningún tarugo ni ninguna herramienta en el interior, es rellenar parcialmente con fibra de poliéster. |
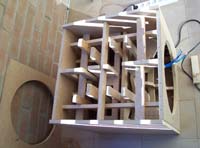 |
La fibra de poliéster no actúa aqui como material absorbente, ya que para frecuencias inferiores a 100 Hz las fibras del estilo de lana, fibra poliéster, fibra de vidrio tienen unos coeficientes de absorción prácticamente nulos, pero a efectos prácticos su contribución es semejante a aumentar el volumen. Estimo que con la cantidad que hay puede aumentar entre un 10 y un 15%.
Se rellenó la mitad posterior de la caja, y sin apretarla mucho. |
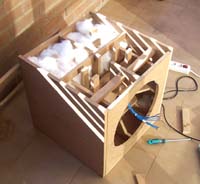 |
Y llegó el momento de cerrar definitivamente la primera caja. Generosidad con la cola y con los tornillos.
Una vez comprobado que la caja cabía bien en el interior de la segunda caja superponiendo los tableros, se procedió a ensamblar dicha caja. Es una caja que no irá anclada en ningún punto a la caja interior, ésta irá "suspendida" dentro de ella. Para ello, como el fin es evitar la transmisión de vibraciones entre una y otra, empleamos un material poco coherente entre una y otra, eso será lo que "sujete" la caja interior. Lo ideal es arena, pero plantea problemas obvios, por lo que decidí usar moqueta. Aqui no hay playa. |
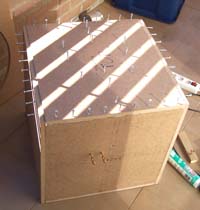 |
Desde luego fue muy sencillo, en dos horas estaba ya montada, pero al comparar la solidez de la caja reforzada con la de la caja exterior se pudo apreciar de sobra la excelente y necesaria función de los refuerzos. En vez de poner un tornillo cada 5 cm como en la interior, los puse cada 10 cm.
No llevará ningún tipo de tratamiento. |
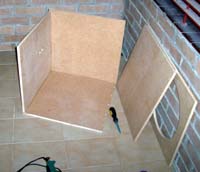 |
Para los conectores, como en principio no se puede dejar ninguna parte sólida que haga contacto con la caja interior, se hicieron unos agujeros más grandes de lo debido para poder sacar por ahí los conectores al exterior.
Aquí el número de tornillos empleados fue mucho menor, unos 60 para toda la caja exterior. Esta caja no va a soportar las presiones interiores tan elevadas que va a soportar la caja interior. Tampoco requiere estar sellada, se comporta símplemente como una pantalla acústica que impedirá a la caja interior radiar sonido al exterior. |
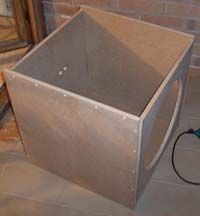 |
Comenzamos a forrar de moqueta la caja interior. Como en el monitor, usé moqueta de polipropileno pegada diréctamente a la caja con cola de contacto. Es imprescindible hacerlo en un lugar ventilado si no se quieren ver elefantes rosas o pitufos (los expertos coinciden en que son alucionaciones recurrentes), antes de la siesta y la terrible resaca que deja inhalar pegamento, aunque se haga de manera involuntaria.
Es una caja interior, por lo que el acabado no es en absoluto una preocupación. |
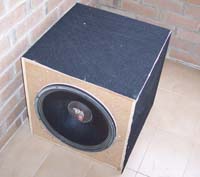 |
Si es más importante que los trozos de moqueta de los laterales tapas superior e inferior se extiendan por la parte trasera de la caja, ya que entrará así en la caja exterior, con la parte trasera primero. Esto es así por los conectores, sobresalen y es la única manera de encajarlas.
A la derecha podemos ver las dos cajas. Llegados a este punto debo decir que el tamaño es más bien mostruoso, pero el que algo quiere algo le cuesta, no se puede pretender reproducir 20 Hz a un volumen razonable y THD por debajo del 10% con cualquier altavoz, y tampoco con cualquier caja. Por mi forma de ver las cosas, a nivel de resultados no existen los términos medios porque las soluciones a medias no son soluciones. ¿quiere buenos graves? no se quede a mitad. |
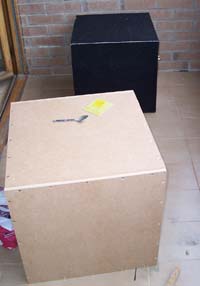 |
Cuando despúes de mucho trabajo se ve una caja tan horrorosa como la foto de la derecha suele afectar a la moral, pero ya son bastantes cajas las que llevo en mi haber y asusta menos. Total, es una caja interior.
Debo desaconsejar completamente la cola de contacto transparente para trabajar con DM, se absorve demasiado rápido y hay que dar una capa sólo como selladora. Aconsejo mejor la cola de contacto de toda la vida, la de color marrón claro-naranja. |
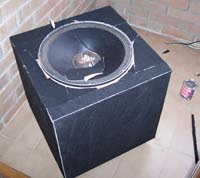 |
Ahora viene la tarea de terminar y dar el acabado a la caja exterior.
En un principio pensé en forrar toda la caja de cuero negro, pero luego pensé que podía quedar demasiado sado, así que pensé mejor en chapar la caja con hoja de roble y luego teñirlo de color caoba oscuro.
Hice unos recortes en el frontal para facilitar la extracción del altavoz en caso de que fuese necesario. |
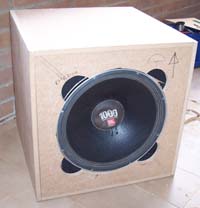 |
También pinté esta parte del frontal, para evitar que se quedasen partes "indiscretas" a la vista por los huecos que el frontal (lo añadiremos luego) no tape. |
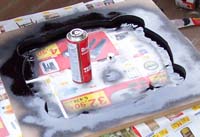 |
A la hora de chapar es importante que la superficie sea lo más lisa posible, y por esto es necesario rellenar los agujeros y desniveles con pasta de madera. Cuando se seca reduce el volumen bastante y es necesario o bien poner un buen pegote y luego lijar o bien hacer varias aplicaciones. |
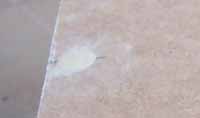 |
A pesar de la precisión del corte, a veces quedan pequeñas irregularidades que también es necesario allanar. No es necesario que quede perfecto, símplemente liso, se puede utilizar también el cepillo eléctrico, con cuidado de no hacer pasar las cuchillas por encima de los tornillos. |
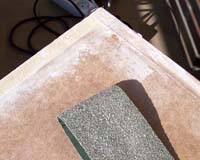 |
Para pegar es conveniente usar cola de contacto. Tiene el inconveniente de que una vez pegado ya no se puede ni mover ni despegar, pero es mucho mejor que utilizar cola blanca, ya que esta arquéa la chapa de madera, hay que utilizar mucho peso para que quede bien pegada y tarda varias horas en secar.
Conviene empezar a pegar desde un punto hasta los demás, frotando todo con un trapo que no suelte pelusa y que no se enganche en las astillas. Cuatro manos pueden ser útiles. |
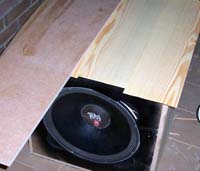 |
Este es el cajón una vez chapado. Queda lijar con lija de grano muy fino para dar un acabado suave, eliminar las imprefecciones y los pelillos de la madera, así el tinte no se acumulará alrededor de ellos.
La última lijada es preferible hacerla a mano, y con una lija lo más gastada posible, así da un tacto muy suave a la madera, y facilitará el barnizado. |
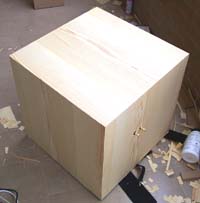 |
Es normal que queden algunas burbujas. Es posible rellenarlas de pegamento inyectándolo diréctamente con una jeringuilla.
Las agujas más finas son las utilizadas para insulina, el pegamento pasa bien a través de ellas aunque hay que hacer un poco de fuerza y al principio, hasta que se pega la aguja a la jeringuilla conviene sujetarla. |
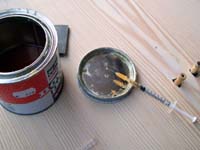 |
La técnica es muy simple. Clavar la aguja de lado para que no se clave en el MDF, y que el pegamento rellene generosamente el hueco.
Luego hay que apretar, y muy posiblemente sobrará pegamento que saldrá por el orificio, y que hay que limpiar porque si no quedarán manchas blancas cuando demos el tinte. |
 |
Para agilizar el secado del pegamento y hacer que la madera se moldee mejor, se puede utilizar una plancha.
Conviene hacer una prueba de temperatura con algún trozo sobrante, para evitar que queme la madera, pero se debe tener en cuenta que una temperatura muy baja hará que la madera no se adapte a la forma y que tarde más en secar.
Consejo para aumentar SAF: limpiar la plancha. |
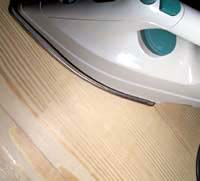 |
A la derecha se pueden observar los efectos del tinte. La primera capa siempre da un aspecto desolador, pero no hay que desaminarse, cuando se barniza y se lija el aspecto es mucho peor...
La obligada segunda capa de tinte siempre mejora el aspecto, aunque el resultado del tinte aplicado no me gustó. En posteriores cajas me plantearé usar una mezcla de anilinas, así se puede elegir el color y es infinitamente más barato. |
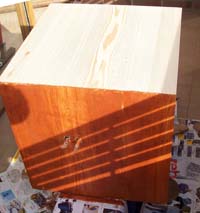 |
Afortunadamente, tras dos manos y un lijado suave con la lana de acero más fina dí una capa de barniz con tinte color caoba.
Desde ese momento el color se ajustaba mucho más a lo que esperaba de la caoba. Aunque parezca asombroso, (el tinte era un tinte al agua, sin selladora ni nada) sólo fue necesario dar una mano de barniz. |
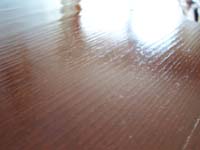 |
El resultado se puede ver en la foto de la derecha y en la inmediantemente superior. Nunca había conseguido un acabado así símplemente con una sóla mano de barniz. en la foto se puede ver cómo no quedaron burbujas ni pelos de la madera (me dejé alguno de la lana de acero, pero no se ven). Es curioso ver que el propio barniz respeta el relieve de la beta, incluso el poro.
Pinté con un rodillo especial para lacar, dando una mano fina y pasando suave y muy lentamente el rodillo hasta conseguir que no quedaran burbujas. |
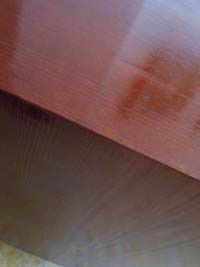 |
Éste es el aspecto de subwoofer casi terminado, a falta de hacer un frontal.
Finalmente decidí hacer un frontal forrado de cuero acolchado. Demasiadas rectas, demasiado volumen. Cuando no se tiene delante es difícil imaginar su tamaño. Con un volumen tan exagerado me parecía interesante dar un aspecto voluptuoso, como las esculturas de Botero. |
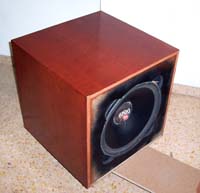 |
Para ello empleé un panel de 4mm de multicapa, cortado con las medidas adecuadas. Dejé que se superpusiera al chasis del altavoz.
De ésta manera sólo se verá la suspensión y el cono. |
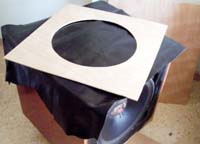 |
Tras cortar la pieza de cuero hice un corte circular con un cutter, y dejé varios cortes a espacios regulares para poder pegar el interior. Es cuero de casi 3mm de espesor y es bastante difícil de trabajar. Utilicé cola de contacto para pegarlo. |
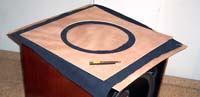 |
En el detalle se puede ver el tipo de corte realizado. No use tijeras, es más sencillo con el cutter, y se puede cortar sobre la misma pieza de multicapa sobrante. |
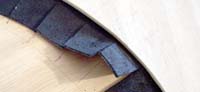 |
Una de las ideas iniciales era que se pudiese sacar el altavoz en caso de que fuese necesario, por lo que el frontal debía ser extraíble. Pensé en varios sistemas, y llegué a la conclusión de que el belcro era lo idóneo para poder retirar el frontal. Pensé en imanes y en otro tipo de tacos. |
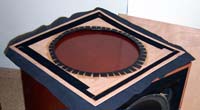 |
Rellenar no es sencillo y menos con un cuero tan grueso. Se usa fibra de poliéster, que es el uso original de este material, por eso lo venden los tapiceros.
Se debe hacer poco a poco, ir metiendo trozos pequeños de fibra y empujar hasta que quede firme, con una regla por ejemplo. El pegado de los laterales se debe hacer a medida que se va rellenando, y preferiblemente en trozos pequeños, si no es imposible acceder cómodamente a todos los rincones |
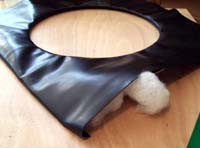 |
Este es el aspecto del interior del frontal. |
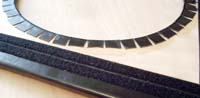 |
Bueno, ha costado varios meses (para mi es una eternidad) pero finalmente está construído.
En estos momentos sólo queda hacer las mediciones pertinentes para ajustar el filtro activo.
En la foto se puede ver "la familia". Los V3, el monitor y el subwoofer Supra. Desde que empecé con la electrónica hace ya unos años sólo he hecho dos altavoces para mí, y son el monitor y este subwoofer.
Pero habrá más. |
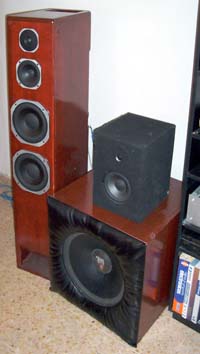 |