CHASIS PARA ETAPAS
INTRODUCCIÓN
Es una preocupación común la de hacer un chasis bueno,
bonito y barato. 3B. Éste diseño de chasis reúne
las tres B's y tiene escasas restricciones.
Mediante el uso de perfiles de carpintería de aluminio se pueden
obtener las partes que conforman éste chasis y su presupuesto
es de aproximadamente 10 euros, si tenemos en cuenta que los chasis
comerciales cuestan entre 60 y 180 euros es una inversión irrisoria
en comparación con los resultados, muy aceptables a nivel estético.
El coste depende ovbiamente del tamaño y la complejidad añadida.
inicio
MATERIALES
Los materiales del chasis se pueden obtener principalmente en carpinterías
de aluminio. Se trata de usar perfiles estándar y planchas de
aluminio, es la clave para tener un coste bajo en los materiales. Otra
de las claves es utilizar el radiador como parte de la caja, concretamente
los laterales.
Los conectores se pueden encontrar en tiendas de electrónica
y audio o reparación de altavoces, en cualquier sitio donde distribuyan
Monacor.
Chasis.
La lista de componentes para el chasis es:
Cantidad
|
|
Concepto
|
2
|
|
Perfil en L 440 x H x 40
|
2
|
|
Perfil en L H x 20 x 20
|
1
|
|
Plancha aluminio 240 x 240 x 1.5
|
8
|
|
Tornillos cabeza Allen negros M5 x 10
|
8
|
|
Tornillos cabeza Allen niquelados M5 x 10
|
16
|
|
Tuercas M5
|
8
|
|
Arandelas anchas M5
|
6
|
|
Tornillos M3 x 10 cabeza plana avellandada
|
6
|
|
Arandelas M3 ó M4*
|
6
|
|
Tuercas M3
|
4 (3**)
|
|
Pies
|
- H es la altura deseada.
- Todas las medidas son en milímetros.
- M5 significa rosca métrica 5.
- * Es difícil encontrar arandelas de métrica 3, las
de métrica 4 valen.
- ** Para conseguir que el amplificador sea más estable mecánicamente
se pueden usar 3 pies en vez de los 4 habituales, de ésta manera
no se balancea ¿conoce alguna silla de 3 patas que "baile?
No es imprescindible usar tornillos de cabeza Allen, pero estéticamente
son los más adecuados. También se puede recurrir a tornillería
cromada pero es difícil de encontrar y cara. En la foto se pueden
ver gran parte de los componentes necesarios.
Cuando encarguemos las piezas de aluminio debemos exigir que
el frontal no tenga ninguna raya. Debemos advertir que no pagaremos
por un frontal rayado. Tampoco debemos incordiar demasiado porque
las carpinterías de aluminio suelen tener largas listas
de espera y también ellos están en condiciones de
negarse o dar plazos exagerados ya que nuestra inversión
será irrisoria comparada con sus trabajos habituales, aparte
de tener una cierta ética.
|
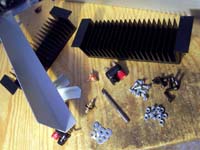 |
Conectores.
La lista de conectores habitualmente externos a la etapa es:
Cantidad
|
|
Concepto
|
1
|
|
Hembra RCA chasis aislada roja
|
1
|
|
Hembra RCA chasis aislada negra
|
2
|
|
Conectores aislados altavoz
|
1
|
|
Conector AC 220V ~ 10A
|
1
|
|
Interruptor AC 220V ~ >4A
|
La elección de los componentes queda a la elección del
usuario. En este punto debemos señalar que no por poner conectores
de una calidad extrema la etapa va a sonar mejor, pero un contacto deficiente
o un amperaje nominal bajo si que pueden ir en detrimento de la calidad
de sonido. En este sentido es necesario dimensionar correctamente y
no es habitual hacerlo bien. Sobredimensionar es una opción recomendable,
pero debemos ser realistas: los niveles de escucha habituales no suelen
suponer más de 10W y esto significa poco más de un amperio,
es una carga fácil para cualquier tipo de conector.
Un conctacto oxidado supone una degradación de la señal
por la gran presencia de microrectificadores Schottky, cuyo efecto
es una degradación en alta frecuencia y señales
de baja intensidad. También aumenta la resistencia del
contacto por la menor superficie útil. Por eso se suele
recurrir a contactos bañados en oro, pero esto ni es la
panacea ni una condición necesaria. Muchos conectores bañados
en oro llevan una capa meramente testimonial y se acaban oxidando
tras dos años, lo que no hace ganar nada sobre un conctacto
niquelado, salvo que se suelda un poco mejor en baños de
oro.
|
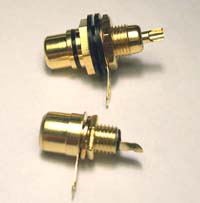 |
Fíjense en un detalle muy simple: los buenos conectores RCA
y XLR de aire sólo llevan baño de oro en el contacto.
El oro es caro, hacer un buen baño también; es mejor tener
todo el oro concentrado en el contacto que distribuido por toda la pieza.
Es más importante la calidad del contacto que el material. En
el caso de materiales susceptibles a oxidación (níquel
y plata) se requiere un cierto mantenimiento, puede ser tan simple como
meter y sacar los conectores varias veces (para limar el óxido)
o como usar limpiadores para metales, hacerlo una o dos veces al año
es suficiente si no vive en zonas costeras, donde la humedad y la presencia
de sal aceleran la oxidación. Los limpiadores de plata no son
compatibles con el resto de metales, y viceversa.
Sobre los conectores de altavoz, no utilice nunca contactos
de pinzas, la superficie útil del contacto es muy baja
y se pueden soltar. Utilice siempre conectores de rosca o banana,
los hay de muchos precios y amperajes pero es obvio que la presión
ejercida por un tornillo es mucho mayor que la que puedan ejercer
cualquier otro anclaje mecánico. Esto deformará
el metal del cable (habitualmente cobre o plata) y la superficie
de contacto será mayor. La difusión de oxígeno
será menor también. Con las roscas es perfectamente
posible utilizar conectores "Y" o de oreja.
|
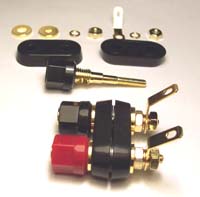 |
En cuestión de bananas, debo decir que las bananas estándar
bañadas en oro tienen una calidad muy pobre. Comparen por
sus propios medios la solidez del contacto entre una banana estándar
niquelada y una supuesta "high-end", que empieza a tener
síntomas de oxidación. El contacto lo hacen unos
hilillos sobre una pieza móvil. En la estándar utilizada
en electrónica general el contacto lo hacen 6 hilos de
bastante grosor y mayor resistencia mecánica.
|
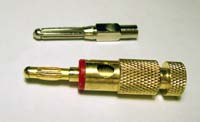 |
La fuerza que hay que hacer para liberar uno y otro es muy diferente,
da una idea de la calidad del contacto. Salvo por comodidad o necesidad,
recomiendo prescindir de las bananas. He usado regletas de empalme de
electricista con mejores resultados.
A nivel de construcción, es mucho mejor utilizar conectores
aislados que aislar nosotros el conector por otros medios (placas de
plástico, fibra de vidrio...) En conectores de altavoz se pueden
usar pasamuros, son unas piezas de plástico que encajan en un
agujero y aislan el chasis del conector, pero en hembras RCA no existe
esa opción. Merece la pena pagar un poco más por la comodidad
y simplificación añadida.
Herramientas.
El taladro es imprescindible, con un juego de brocas bien surtido.
Sobre las demás herramientas, dependerá de la cantidad
de veces que las use, el aluminio es fácil (aunque laborioso)
de cortar agujeros de cualquier tipo con sierra de marquetería
y pelo de metal, y las roscas se pueden hacer con tornillos de rosca
de chapa. Las demás herramientas recomendadas son:
Fresa para cortes irregulares. Se trata de una fresa que se puede
utilizar con el propio taladro para hacer agujeros de forma irregular,
en fibra de vidrio, plástico, aluminio y chapa. Es un poco
difícil de manejar pero es muy útil especialmente
en los casos en los que no podemos trabajar con sierra.
|
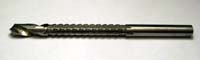 |
Terrajas: Para hacer roscas en el propio chasis o en los radiadores.
Los tamaños y roscas recomendados son M5 (chasis) y M3
(radiadores). Caras pero útiles.
|
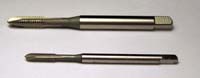 |
Fresas para agujeros redondos. Su coste es alto y sólo
recomiendo comprarla si se van a hacer agujeros de gran tamaño
repetidamente (XLR por ejemplo). Para algunos agujeros esporádicos
se puede utilizar la primera fresa.
|
|
inicio
Anclaje de las etapas al radiador.
Como primer consejo, es recomendable hacer los agujeros necesarios
para acoplar el radiador al chassis antes de proceder al anclaje de
la etapa.
Antes de anclar la etapa al radiador es recomendable comprobar
que la etapa funciona correctamente. Es un poco paradójico
porque no es posible comprobar que una etapa funciona correctamente
si no se ha probado que la polarización es estable, pero
puede servirnos cualquier trozo de aluminio para probar. Peor
será tener que hacer nuevos agujeros, soldar y desoldar.
Un aspecto importante es que los transistores de potencia tienen
una parte metálica por detrás, conectada habitualmente
al colector/drenador. Ésto se hace para que el transistor
pueda disipar mejor el calor, ya que el metal (cobre) tiene una
conductividad térmica mayor que cualquier otro material
que sea aislante eléctrico.
Lo primero que debemos hacer es doblar las patas de los transistores
para que queden a la altura del final de la PCB. Si no hacemos
ésto, el tornillo partirá los transistores y será
necesario cambiarlos
|
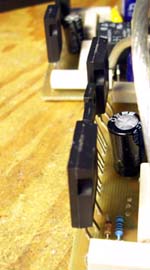 |
Para marcar los agujeros podemos y debemos emplear la propia
etapa como guía. La mayoría de los rotuladores permanentes
son demasiado gruesos para marcar a través de los agujeros
de los transistores de potencia, por lo que un simple portaminas
puede servir mejor.
Se debe tener ciudado de hacer las marcas en perpendicular y
no borrarlas luego.
|
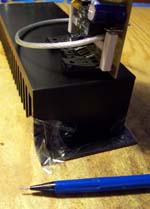 |
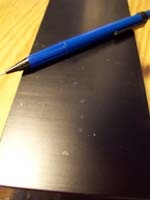 |
Para taladrar debemos marcar el centro del agujero con un punzón
específico para estas tareas llamado granete. La broca
debe estar humedecida con aceite, en principio vale cualquier
tipo, y debemos humedecer la broca tantas veces como sea necesario.
Taladraremos a baja velocidad. Debe salir una espiral de aluminio.
Si salen virutas, o bien se afila la broca o se pone más
aceite. El aceite es necesario porque cuando el aluminio se calienta
se pega a la broca y la tapona.
|
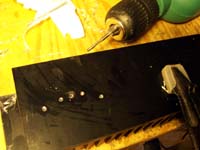 |
Para hacer las roscas se deberían emplear tornillos de
rosca de chapa, pero hacer una rosca "a mano" en un
radiador tan grueso es un problema serio. Se pueden utilizar terrajas
de rosca métrica 3, pero se debe tener en cuenta que no
se puede meter y sacar el tornillo en la rosca más de 5
veces, el aluminio es débil.
|
 |
Para ello habremos hecho un agujero de 2.5mm y sumergiremos la
terraja en aceite. Se puede utilizar el taladro pero siempre a
bajas revoluciones. Si el taladro no es reversible será
difícil sacar la terraja sin partirla. Si no se usa aceite
se puede partir la terraja y se quedará dentro del agujero.
Por supuesto, ni sueñe con taladrar la terraja como podría
hacerse con un tornillo roto dentro de acero: las terrajas son
muy duras y el aluminio muy débil.
|
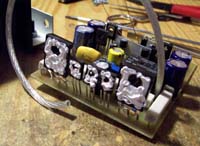 |
Una vez hechos los agujeros pondremos silicona termoconductora
en los transistores. Recomiendo usar la jeringuilla en vez de
los botes, mancha todo lo que toca.
Luego pondremos los aislantes de mica; se debe recortar si es
necesario: no deben solaparse ni mucho menos quedarse a mitad
de otro transistor. En los TO-3, TO-220 y algunos otros encapsulados
se debe aislar la parte metálica del tornillo mediante
arandelas de nylon.
|
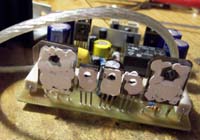 |
Y ahora volveremos a dar silicona termoconductora en la otra
cara del aislante de mica.
Existen otros aislantes, muy cómodos y limpios, son las
almohadillas termoconductoras, son de color gris y de un material
parecido a la goma. Su problema: Tienen mayor resistencia térmica
que la mica y la silicona. También hay versiones de almohadillas
que no aislan, su resistencia térmica es más baja
pero no sirven para etapas de potencia de audio
|
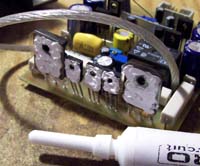 |
El siguiente paso es colocar los tornillos de rosca métrica
3 o rosca de chapa. El tornillo debe entrar con holgura en el
transistor, si no entra limpiamente, lo partirá al mínimo
esfuerzo.
Primero introduciremos unos 3mm de cada tornillos, antes de apretarlos
todos deben estar metidos en su agujero. También es conveniente
hacer una segunda aproximación y dejarlos todos metidos
a falta de 1-0.5mm.
|
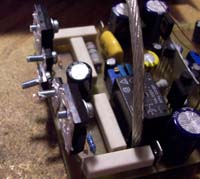 |
Esto hace que encajen mejor en el hueco y reduciremos las probabilidades
de partir algún transistor. Los transistores deben quedar
perfectamente paralelos al radiador, no puede quedar ninguna rendija,
esto sería como si no hubiera contacto térmico y
acabará quemándose.
Por último, es estrictamente necesario comprobar que los
transistores no tienen contacto con el radiador. Como hemos comentado
antes, los transitores suelen tener el colector/drenador en contacto
con la parte metálica de atrás, así disipan
mejor el calor del interior.
|
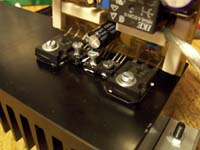 |
Para hacer esta comprobación engancharemos una de las sondas
del polímetro en modo diodo al radiador. Luego comprobaremos
la continuidad tocando otras partes del radiador o los tornillos. Puede
suceder que esa sonda no haga contacto y por ello pensemos que están
todos bien colocados.
Tocaremos con la otra sonda en las patas centrales de todos los transistores,
y ninguno debe dar ni continuidad. Normalmente si el primero no da continuidad
o no da números raros no hay ningún problema; los números
raros (entre 500 y 1500) suelen indicar que hay otro transistor en contacto
con el radiador.
Si se supera la prueba satisfactoriamente ya está listo para
ensambarse en el chasis, aunque si quiere puede comprobar que funciona,
en caso de haber partido algún transistor se ahorrará
desmontar.
inicio
MONTAJE
Lo básico:
Es vital entender y poner en práctica que para trabajar rápido
y bien hay que poner los medios necesarios. Lo primero es trabajar con
herramientas adecuadas, lo segundo es trabajar con comodidad y lo tercero
es una buena planificación.
- Las herramientas adecuadas permiten hacer en poco tiempo, con mejores
resultados y con comodidad lo que de otra manera tardaría tiempos
entre 1 y 250 veces: ejemplo: crimpar 10 cables (15 seg) frente a
soldarlos (1 hora). Hacer agujeros de diámetro medio (15-30mm)
en acero: con fresa 3 minutos, con sierra de calar 3 minutos y una
chapuza; sierra de marquetería: >30 minutos.
- Trabajar con incomodidad siempre produce errores: Las conexiones
y tornillos poco accesibles pueden quedar mal ensamblados, las herramientas
pueden dañar otros componentes; las partes que dificultan la
visión impiden ver si la conexión está bien o
mal hecha, incluso impiden ver si está hecha, también
pueden tapar fragmentos metálicos que producen corotocircuitos.
La incomodidad y la dificultad generan nervios y fatiga, y los errores
son el siguiente paso: conectar las alimentaciones al revés,
hacer cortociruitos, dejar sin hacer comprobaciones importantes...
- La necesidad de una buena planificación es obvia, si por
ejemplo la altura de los condensadores supera la altura del chasis
ya no se puede tapar, o si no hay espacio suficiente para introducir
un módulo, ¿Qué se tiene que hacer? otro chasis.
Colocación de los bloques.
La colocación más obvia de los bloques parte de
las necesidades estéticas y prácticas. En el frontal
no puede ir la alimentación de 220V, no es estético
y es peligroso. Los radiadores no pueden ir en el centro, sólo
servirá para calentar la caja y reducir la eficiencia del
radiador, por lo que deben ir en el exterior.
Si hay dos, en los laterales, si hay uno, en la parte trasera
o en un lateral. El transformador debe estar lo más alejado
posible del resto de los componentes, especialmente entradas y
etapas. También los cables que entran y salen de él.
|

Distribución recomendada en una etapa monocanal
|
Lo habitual es que en la parte delantera sólo estén
los controles interactivos, en los que se encuentran un LED indicador
de encendido, el interruptor de encendido, control de volumen,
controles de tono, selector de canal y demás elementos
de ajuste en tiempo real. Conectores y ajustes fijos, en la parte
de atrás.
Mi experiencia me dicta que dentro de un chasis, cuanto más
fácil sea extaer un bloque, mejor: ahorrará tiempo
y esfuerzo.
|
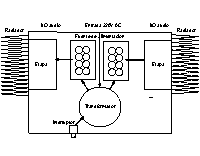
Distribución recomendada en una etapa estéreo
|
Por eso recomiendo encarecidamente ensamblar la fuente de alimentación
y los circuitos de control en una plancha de aluminio. Montaremos todo,
comprobaremos que funciona y entonces ensablaremos el bloque completo
(plancha incluída) dentro del chasis. Cuantas menos conexiones
tengamos que hacer de vez, mejor. Uno de los algoritmos que mejor resultado
dan en diseños complejos es el "divide y venderás":
modularidad, bloques. Nuestra inteligencia no nos permite concentrar
nuestra atención en un gran número de factores, cuantos
menos factores haya que tener en cuenta, menor probabilidad de error.
Ventilación.
Dejar grandes huecos mejora de forma muy significativa la ventilación
del interior; ésto alarga la vida de los condensadores en una
proporción del doble de vida por cada reducción de 10
grados centígrados o grados Kelvin.
En dos rejillas iguales, con una superficie metálica del 50%
sobre el total, cuanto mayores sean los agujeros, mayor será
la ventilación. Debemos tener una mínima consideración
sobre la dinámica de fluídos: cuanto menor sea el diámetro
de los agujeros, mayor será la resistencia que ofrezcan al flujo
del aire. Mejor pocos agujeros pero grandes que muchos y pequeños.
Esto va en detrimento de la seguridad, cuanto mayores sean los agujeros,
mejor pasarán los dedos y existen dos riesgos: se almacenan grandes
energías y existen partes a gran temperatura en el interior.
Si en su entorno existen personas susceptibles de meter los dedos (niños,
manazas, gatos,...) deberá tenerlo en cuenta y proteger el interior
de la etapa convenientemente, mediante una rejilla más fina o
dificultando el acceso. Dificultar el acceso a un gato es una tarea
complicada.
Una descarga produce quemaduras leves, pero si está encendido
puede causar la muerte. Afortunadamente el 90% de la población
somos diestros, el corazón se sitúa en el lado izquierdo,
en pleno camino eléctrico entre el dedo (terminal 1) y el suelo
(toma a tierra). No es un chiste, a nivel eléctrico somos una
resistencia. Esto no implica que si tocamos con la derecha no podamos
sufrir un paro cardiaco, pero se reducen las probabilidades.
Para terminar, probabilidad no implica que algo suceda o no, significa
que cuando se repita infinitas veces habrá "X" % de
éxitos y (100-"X") % fracasos (Ley de Laplace). Da
igual que la probabilidad sea del 0,0001%, puede tocarle a usted mientras
999.999 personas se salvan.
EJEMPLO Y DIMENSIONES.
Empleamos como ejemplo una etapa Ultra de 25+25W.
La plancha de aluminio sobre la que se ensabla la fuente y los circuitos
de control mide 240 x 240 mm. La profundidad debe ser igual o levemente
menor (>1cm) de la longitud de los radiadores, aunque el ancho se
puede variar según las necesidades. Antes de montar, se debe
comprobar que funciona.
Utilizamos los perfiles con forma de L de 20 x 20 mm como unión
en forma de escuadra entre el radiador y el frontal y trasera.
Los agujeros que unen el radiador con ésta pieza y los
que unen el frontal no deben estar a la misma altura, es conveniente
dejar una separación mínima de 8mm, si coinciden
los tornillos no podremos meter ni apretar las tuercas, tal vez
tampoco los tornillos.
|
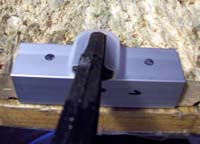 |
Debemos hacer los 4 agujeros que lleva cada pieza antes de montarla.
Los acoplaremos al interior del radiador mediante los tornillos
M5 Allen negros y tuerca, no es necesaria arandela.
|
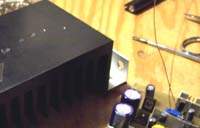 |
En este caso el interruptor se pone detrás porque en mi caso
controlo el encendido de todas las etapas desde un interruptor general,
por lo que en el frontal sólo existe un agujero de 5mm para colocar
el LED indicador de encendido y los 4 agujeros por los que se unirá
a los radiadores. En la parte inferior se hacen los agujeros que sujetarán
la plancha con la fuente de alimentación y control y se hace
un avellanado, si no se dispone de herramienta se puede hacer con una
broca de mayor tamaño y mucho cuidado de no traspasar ni agrandar
el agujero. Antes de taladrar marcaremos los centros de los agujeros
con el punzón o el granete, o con un clavo, tornillo,... Puede
ser recomendable forrar el frontal con cinta de embalar o cinta de carrocero
para evitar que se ralle.
La parte trasera es la más laboriosa en este chasis y en general
en todos, por la cantidad y dificultad de los agujeros. Debemos tener
cuidado de que los conectores no toquen en las etapas o la fuente. Una
vez hecho un agujero no se puede tapar, en la parte trasera al menos
es permisible porque no se suele ver.
Para una etapa de potencia, la mejor colocación es poner
cada hembra RCA y la respectiva salida de los altavoces lo más
cerca posible de la etapa de ese canal, así minimizamos
la longitud del cable y la posibilidad de recoger ruidos. Así
marcaremos todos los agujeros (simétricamente) y procederemos
a taladrar, no tiene ningún misterio. Una vez hechos los
agujeros, fresaremos los agujeros irregulares para el conector
de AC y el interruptor (sólo en este caso)
Para ello dibujaremos el perfil del agujero, y aprovecharemos
que la fresa empleada puede hacer su porpio agujero de entrada.
No es necesario utilizar una fresadora, para unos tamaños
tan reducidos con un poco de práctica se puede utilizar
el taladro. No es necesaria una gran precisión y con la
práctica se pueden hacer líneas suficientemente
rectas. Se puede ver que no es "mi primer agujero",
antes utilizaba la sierra de marquetería.
|
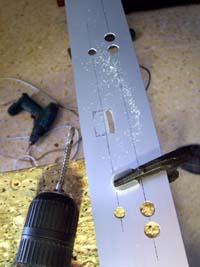 |
Taladraremos también los agujeros que permiten unir la parte
trasera a los radiadores, y los que unirán esta parte a la plancha
de la fuente.
Una vez taladrado todo, colocaremos los conectores. Para la hembra
RCA, colocaremos una de las arandelas aislantes por fuera y otra
por dentro. No pude estar soldada a nada todavía. Para
los conectores de altavoz, lo mismo, una de las arandelas por
fuera y la otra por dentro, cercionándonos de que encajan
en el agujero. El conector de los altavoces es el ST-922G de Monacor.
|
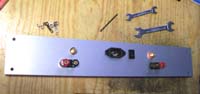 |
Soldaremos también los cables que van del conector de AC al
interruptor, emplearemos conectores Faxton, aunque parezca un desperdicio,
si tenemos que desmontar será más fácil. Se puede
conectar un condensador plástico (preferiblemente polipropileno
clase X2) de 100nF y 400V entre las entradas de la alimentación.
La del medio es tierra, por lo general no se conecta al chasis, y si
se hace, a través de un condensador también de 100nF y
una resistencia de 5W de 10 Ohm. De otra manera inducirá ruidos
en la etapa.
Para el cable de la alimentación de 220V recomiendo usar como
aislante silicona o teflón, resiten altas temperaturas y el de
silicona es sumamente flexible. Del interruptor deben salir dos cables
que irán a la fuente.
Ahora atornillaremos la parte trasera a la plancha de la fuente
de alimentación y control, con los tornillos de M3 y cabeza
plana avellanada. Con un poco de prática pueden quedar
al ras.
Conectaremos la entrada de 220V y luego conectaremos las tierras
pertientes (RCA y retorno del altavoz) con un cable propio para
cada una, lo más alejado posible de los cables de 220V
AC, y con la mínima longitud que nos permita trabajar con
comodidad.
|
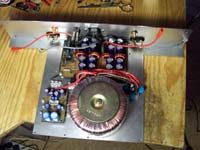 |
Puede ser más importante apantallar estos cables de tierra que
los de señal, al fin y al cabo el par trenzado tiene una gran
inmunidad al ruido pero un cable sólo no. Aunque en diseño
con EMI lo primero que se recomienda es asilar la fuente de EMI, por
lo que es muy recomendable apantallar los cables de 220V AC, más
que los de señal. Por mucho que apantallemos estos cables, para
empezar tienen una gran inmunidad, no sirve de nada si no se apantallan
también las etapas, y en esta situación es más
fácil apantallar el cable de 220V AC.
Las pantallas se pueden hacer pegando papel de aluminio sobre cinta
de embalar (polipropileno) y envolviendo el cable en cuestión,
con el aluminio hacia afuera. Luego se coloca un hilo rígido
en espiral sobre el aluminio, por si se parte, y se forra con algún
tipo de funda: Telfón, silicona o preferiblemente funda termorretráctil,
fácil de encontrar. La pantalla sólo se conecta a tierra
en uno de los extremos.
Una vez conectados estos cables y hechas las pantallas pertinentes
colocaremos el frontal, con los tornillos de M3 y cabeza plana avellanada
que lo unen a la plancha con la fuente y el control.
Y por fin, las etapas. Las acoplaremos con los ocho tornillos
M5 Allen niquelados, con una arandela ancha en el interior.
Si es necesario (en este caso si), también atornillaremos
las etapas al chasis. Usaremos espaciadores de Nylon y tornillos
M3.
Por último, terminaremos de conectar todos los cables
internos y comprobaremos que no hay virutas metálicas o
cortocircuitos en su interior. Luego comprobaremos de nuevo que
funciona. Puede haber sufrido algún golpe o cortocircuito
durante el montaje.
|
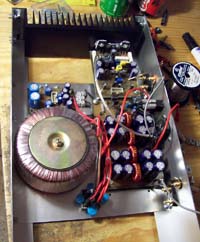 |
SIN TERMINAR, PRÓXIMA AMPLIACIÓN
inicio
|